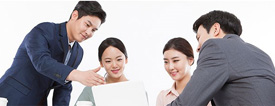
Color masterbatch variety and grade
Quality classification
1, according to the carrier classification: such as PE color masterbatch, PP color masterbatch, ABS color masterbatch, PVC color masterbatch, EVA color masterbatch and so on.
2, according to the purpose of classification: such as injection color masterbatch, blown color masterbatch, spinning color masterbatch.
Classification of grades, such as
1. Advanced injection color masterbatch: used in cosmetic packaging boxes, toys, electrical enclosures and other advanced products.
2. Ordinary injection color masterbatch: used for general daily plastic products, industrial containers, etc.
3. Advanced blown film color masterbatch: used for blow molding coloring of ultra-thin products.
4, ordinary blown film color masterbatch: used for general packaging bags, woven bags of blow molding.
5, spinning color masterbatch: used for textile fiber spinning coloring, color masterbatch pigment particles, high concentration, strong tinting strength, heat resistance, light resistance.
6, low-grade color masterbatch: used to manufacture low-grade products that do not require high color quality. Such as trash cans, low-level containers, etc.
7. Special color masterbatch: It is a color masterbone made of the same plastic as the carrier according to the plastic type specified by the user for the product. For example, PP color masterbatch and ABS color masterbatch respectively use PP and ABS as carriers.
8. Universal color masterbatch: A resin (often a low melting point PE) is also used as a carrier, but it can be applied to the coloration of other resins than its carrier resin.
The difference between universal color masterbatch and special color masterbatch
Dedicated color master
It is a color master made of the same plastic as the carrier according to the plastic type specified by the user for the product. For example, PP color masterbatch and ABS color masterbatch respectively use PP and ABS as carriers.
Universal color masterbatch
A resin (often a low melting point PE) is also used as a carrier, but it can be applied to the coloration of other resins than its carrier resin.
The universal color masterbatch is relatively simple and convenient, but has many disadvantages. It is recommended that you use a special color masterbatch.
Why are many companies not producing universal color masterbatches?
Most formal color masterbatch companies in the world generally do not produce universal color masterbatches. There are many disadvantages to the universal color masterbatch. In fact, the “universal” range of the universal color masterbatch is very narrow, and the technical indicators and economic benefits are also poor.
1. The foresight of the coloring effect is poor. The color masterbatch is used for coloring, and the pigment of the universal color masterbatch exhibits different colors in different plastics, so the coloring effect is less predictable.
2. Affect other properties of plastic products. In particular, it affects the strength, and the product is easily deformed and twisted, which is more obvious to engineering plastics.
Color masterbatch production process
Product name, vulgar name and process technology
Divided into materials: polyethylene, polypropylene, ABS, HIPS / PS, nylon, polyester, polypropylene spinning, pearlescent, PE cable sheathing, communication cable, PE foam, PS foam masterbatch.
According to the function, it is divided into: antistatic, flame retardant, anti-aging, anti-reflection, whitening and brightening masterbatch.
Divided by color: black, white, yellow, green, red, orange, brown, blue, silver, gold, purple, gray, pink, pearlescent, imitation marble (flow pattern), wood grain masterbatch.
There are four ways to process the masterbatch production process.
1. Ink method: As the name implies, it is a production method using ink color paste in the production of masterbatch, that is, a three-roll mill is used to coat a surface of the pigment with a low molecular protective layer. The ground fine color paste is then mixed with a carrier resin, then plasticized by a two-roll mill (also called a two-roll mill), and finally granulated by a single-screw or twin-screw extruder.
2. Flushing method: the pigment, water and dispersing agent are sanded to make the pigment particles less than 1 μm, and the pigment is transferred into the oil phase by a phase transfer method, and then dried to obtain a masterbatch. An organic solvent, as well as a corresponding solvent recovery unit, is required for phase inversion. The process is as follows:
Fine color slurry washing → evaporation concentrate drying → adding carrier → extrusion granulation
3. Pinching method: After blending the pigment and the oil carrier, the pigment is lyophilized to wash the pigment from the aqueous phase into the oil phase by kneading. At the same time, the surface of the pigment is coated by an oil carrier to stabilize the dispersion of the pigment and prevent the pigment from agglomerating.
4. Metal soap method: after the pigment is ground, the particle size reaches about 1μm, and the soap liquid is added at a certain temperature, so that the surface layer of each pigment particle is uniformly wetted by the soap liquid to form a layer of saponification liquid, when the metal salt After the solution is added, it chemically reacts with the saponified layer on the surface of the pigment to form a protective layer of magnesium soap (magnesium stearate), so that the ground pigment particles do not cause flocculation, but protect a certain fineness. . The process is as follows:
Ingredients→stirring→coarse color slurry→three-roll grinding→fine color paste→two-roll plasticating→extruding granulation